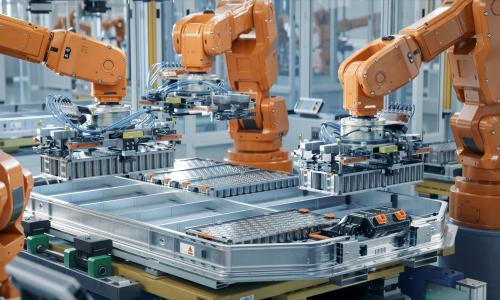
Lithium-ion Battery Manufacturing in India: Revisiting Missing Links
India's lithium-ion battery (LIB) market is experiencing rapid growth, with annual demand expected to increase from 10.8 GWh in 2022 to 160.3 GWh by 2030. Currently, this market is heavily import-dependent, with imports rising from $384.6 million in 2019 to $2.8 billion in 2023. To reduce this reliance, India is ramping up the domestic LIB manufacturing capacity, which is expected to reach 150 GWh annually by 2030, supported by government incentives and private sector investments. This blog explores key initiatives announced to strengthen the resilience of LIB supply chain while highlighting the critical gaps that still need to be addressed.
LIB Supply Chain: Challenges & Policy Support
As of 2023, the domestic manufacturing of LIBs in India has reached 18 GWh. The current focus is primarily on assembling battery packs using imported cells. To enhance domestic cell manufacturing, the Ministry of Heavy Industries has allocated 40 GWh of a targeted 50 GWh capacity under the Production-Linked Incentive (PLI) scheme for Advanced Chemistry Cell (ACC) manufacturing. Furthermore, the fund allocation for this initiative has been increased from ₹12.01 crore to ₹250 crore for the fiscal year 2023-2024. In addition to the national-level support provided through the PLI scheme, several Indian states offer policy support for LIB manufacturers as part of their electric vehicle (EV) policies (see Figure 1).
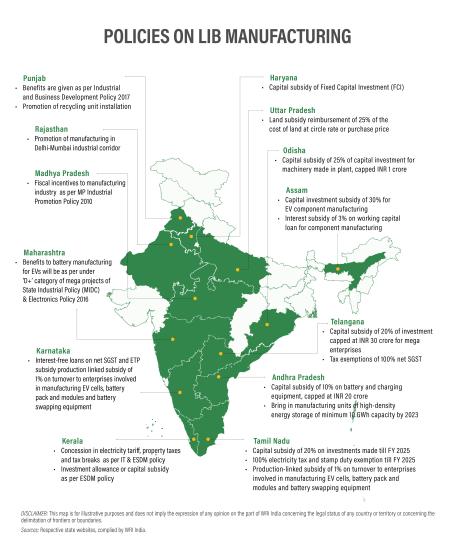
Figure 1: Policy framework adopted by state to promote LIB Manufacturing. Source: Compilation of State EV Policy.
To accelerate the backward integration of the LIB supply chain in India, it is crucial for domestic cell manufacturers to have access to key components like anode active material (AAM), cathode active material (CAM), electrolytes and separators. By 2030, India will require approximately 193,000 tons of CAM annually to produce 100 GWh of LIBs (see figure 2). Currently, limited domestic production, the lack of commercial-scale technology for AAM and CAM, and restricted access to raw materials present significant challenges. However, these obstacles also create opportunities for innovation and collaboration to strengthen the supply chain. Additionally, the development of other LIB pack components, such as Battery Management Systems (BMS) and Battery Thermal Management Systems (BTMS), is essential for domestic advancement.
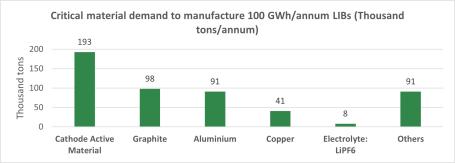
Figure 2: Critical material demand to manufacture 100 GWh/annum LIBs by 2030.
Source: NITI Aayog
Note: LIB’s share is distributed as follows:
Lithium Iron Phosphate (LFP) - 60%, Nickel Manganese Cobalt (NMC) - 25%, Lithium Cobalt Oxide (LCO) - 15%
Raw Materials for LIB Manufacturing
India heavily relies on imports for key battery materials, such as lithium, nickel, and cobalt, while domestic production is focused on ancillary and precursor materials, including graphite, aluminium, copper, phosphorus and manganese. To leverage the domestic mineral deposits, the Indian government amended the Mines and Minerals Amendment Bill, 2023 that facilitates private sector participation in mineral exploration. As a result, in 2024, the central government successfully auctioned 24 blocks of critical and strategic minerals, including lithium and graphite, for battery production. However, mining activities also come with environmental and socio-economic challenges such as habitat disruption, water contamination and community displacement, which require careful regulatory oversight.
To acquire critical minerals overseas, a joint venture company, Khanij Bidesh India Limited (KABIL) has been established under the aegis of Ministry of Mines, Government of India. Additionally, initiatives such as the National Critical Mineral Mission, with a budget of ₹16,300 crore, aim to strengthen the upstream segment of the value chain — from mineral exploration and mining to processing and end-of-life recovery.
Another source of battery raw material extraction is urban mining, which involves extracting valuable resources from e-waste. India expects ~128 GWh end-of-life (EoL) LIBs to be available for recycling by 2030, offering significant potential for mineral recycling (see Figure 3). Challenges such as inefficient EoL battery collection, lack of data sharing mechanisms and technological limitations hinder urban mining potential. This necessitates improving reverse logistics and implementing a battery data management and sharing framework to effectively trace, collect and recycle EoL batteries.
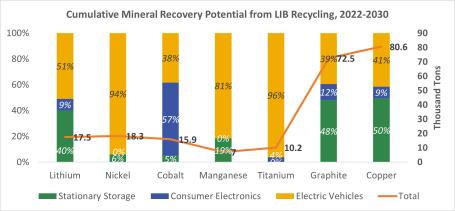
Figure 3: Cumulative Mineral Potential from Recycling of Stationary Application, Consumer Electronics and EV Batteries, 2022-2030. Source: NITI Aayog.
Manufacturing and Recycling Processes
India has expertise in processing battery precursor materials – materials used to manufacture CAMs – such as aluminium, refined copper, manganese sulfate and phosphoric acid. However, it lacks commercial-scale processing capacity for key precursor materials like lithium carbonate. Additionally, the production process for LIB cells involves multiple steps and without strict quality control, scrap generated during the process can exceed the limit of 30%. However, implementing effective quality measures can reduce this to as low as 5%, leading to significant reductions in manufacturing costs and material waste. Advanced automation and the use of artificial intelligence can optimize the production process, reduce scrap rates and enhance overall production efficiency.
Designing a circularity-friendly battery pack is crucial for efficient and cost-effective reuse and recycling. Simplifying the process of disassembly can significantly reduce costs, as it accounts for 2% to 20% of the total battery recycling expenses. Furthermore, innovative solutions must be integrated into current commercial recycling technologies, such as pyro- and hydro-metallurgy, to increase efficiency and reduce environmental impact. Additionally, we need to explore emerging technologies like direct recycling to improve the efficiency and cost-effectiveness of the recycling process.
India currently has an annual LIB recycling capacity of over 60,000 tonnes, but only 50% of this is converted into black mass, which is then exported for further processing. Building domestic processing capacity to convert black mass into battery-grade materials is essential for securing critical raw materials for the local battery manufacturing industry.
Summary & Way Forward
To establish a sustainable battery ecosystem, India needs to address supply chain gaps and integrate circularity throughout various stages of the LIB supply chain. Additionally, it should promote strong research and innovation support for the industry. The following steps can help bridge the gaps in the LIB supply chain:
- Encourage domestic manufacturing of active battery materials, like the PLI scheme for cell manufacturing.
- Create a domestic market for battery-grade materials recovered from black mass, allowing for the reintegration of recycled materials into the LIB supply chain.
- Develop a local industry focused on the mining, processing and refining of battery materials, while advancing research to improve material recovery, reduce waste and minimize environmental impact.
- Support research and innovation to enhance material efficiency and promote circular-friendly battery packs during the manufacturing process.
- Support the domestic development of equipment and technologies for both LIB manufacturing and recycling.
All illustrations by Safia Zahid and Anindita Bhattacharjee/WRI India.
All views expressed by the authors are personal.