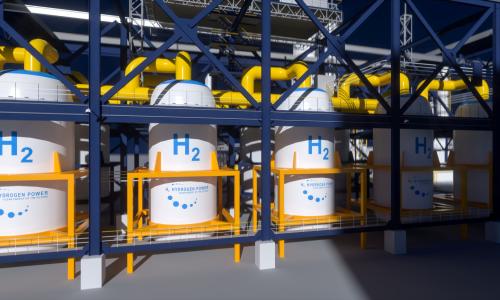
Securing the Supply: Electrolyzers for Green Hydrogen
Green hydrogen, produced via the electrolysis of water using renewable energy sources, is a pivotal solution for decarbonizing industries such as refining, shipping, steel, heavy-duty transport, energy storage and others. Electrolyzers are an essential part of the green hydrogen production process and by 2050, electrolysis could contribute to 50-65% of global green hydrogen production.
Initiatives such as the EU Green Hydrogen Strategy, India’s National Green Hydrogen Mission, and the US Hydrogen Earthshot aim to reduce the cost of green hydrogen to $1 per kg by 2030. However, challenges such as high costs ($5 to $6/kg), reliance on rare materials like platinum and iridium, inefficiencies in production processes, and fragmented supply chains limit scalability. Advancing key electrolyzer technologies — alkaline, proton exchange membrane (PEM), anion exchange membrane (AEM) and solid oxide electrolyzer (SOEC); alongside vertical integration and supply chain optimization — is crucial to overcome these barriers.
This blog focuses on the strategies employed by over 200 original equipment manufacturers (OEMs) to address these challenges and drive innovation in electrolyzer manufacturing.
Expanding Production Capabilities
The IEA’s 2024 report highlights that global electrolyzer manufacturing capacity reached 25 GW annually in 2023 and is set to exceed 40 GW by 2024. By 2030, this figure is projected to surpass the global capacity of 165 GW per year, with significant contributions from China (30%), Europe (20%) and North America (15%). The announced electrolyzer manufacturing capacity, categorized by region and technology, is depicted in the following figure:
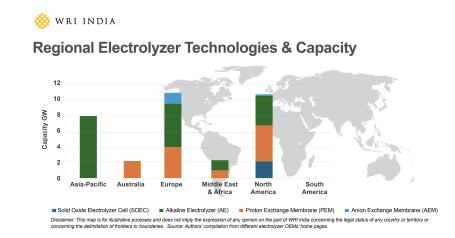
To achieve these targets, OEMs are investing heavily in gigafactories and regional manufacturing hubs. These efforts aim to boost annual production capacities, ensure supply chain resilience and meet the growing global demand.
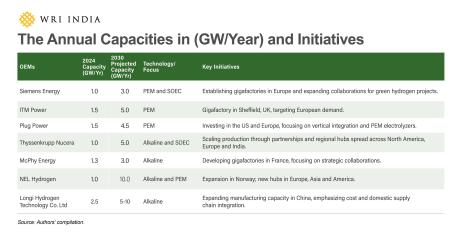
Beyond capacity expansion, OEMs are localizing production to enhance cost efficiency and reduce logistics expenses, along with complying with regional regulations, to strengthen market competitiveness. Companies such as John Cockerill, Plug Power and Cummins are establishing localized manufacturing facilities in different parts of the world, such as Europe, China, the United States and Asia, to better serve these critical markets. In India, notable efforts include Thermax partnering with Ceres for SOEC, L&T’s collaborations with McPhy for electrolyzer manufacturing, and Ohmium's alliance with NTPC to strengthen the domestic production of electrolyzers.
Driving Technological Innovations
Enhancing electrolyzer efficiency, improving operability and reducing CAPEX are key priorities in OEM strategies. The table below presents notable examples of innovations and advancements in electrolyzer technologies by leading manufacturers and OEMs, illustrating their efforts to boost efficiency, lower costs and optimize performance.
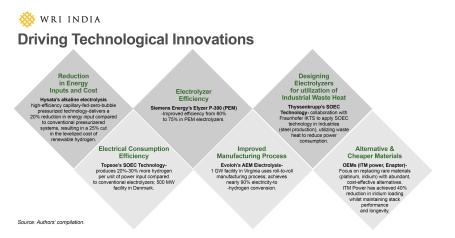
Vertical Integration and Supply Chain Control
The electrolyzer supply chain depends on a limited number of suppliers for critical materials, including platinum-group metals. This contributes to challenges such as price volatility, supply disruptions, inefficiencies and limited scalability. Therefore, adopting the approach of vertical integration in the business strategy is becoming increasingly important for electrolyzer OEMs. Vertical integration refers to a strategy where a company expands its control over multiple stages of its production process, from raw material sourcing to electrolyzer production and operation. By integrating these stages, OEMS can reduce reliance on external suppliers, stabilize costs of key components like catalysts and membranes, and achieve greater efficiency. For instance, Plug Power provides plug-and-play electrolyzer systems, as well as custom-engineered, built-to-order integrated solutions. In addition, it offers hydrogen storage and fuel cell systems, delivering comprehensive green hydrogen solutions. Companies like Cummins and Nel ASA are expanding into both upstream and downstream parts of the supply chain to create a robust infrastructure that can support the rapid scaling of hydrogen technologies. By controlling these critical stages, vertically integrated companies can offer more reliable and scalable hydrogen solutions and help drive the transition to clean energy.
Digitalization and Smart Technology Integration
The integration of digital technologies such as Internet of Things (IoT), Artificial Intelligence (AI), and digital twins is enhancing electrolyzer manufacturing and optimizing product performance. The IoT sensors continuously monitor critical parameters like temperature, pressure, voltage, current density and hydrogen output, ensuring that the electrolyzer operates within optimal ranges. The machine learning algorithms analyze this data to detect inefficiencies and optimize operating parameters dynamically to maximize efficiency and minimize energy consumption. Siemens Energy is integrating IoT and digital twin technologies to monitor and optimize electrolyzer performance and predict maintenance needs. The digital twins are virtual replicas of physical systems that help reduce R&D time and costs by allowing manufacturers to simulate operational scenarios under different conditions. Emerson has also developed digital twin technology to scale up industrial PEM electrolysis. It enables analysis of design scenarios, validation of control strategies and optimization of preventive maintenance practices.
Electrolyzer OEMs’ strategies, including cost reduction through scale, automation, and modular designs, can make green hydrogen more affordable globally. This can, in turn, lower production costs, helping businesses scale quickly and meet rising demands. Strategic partnerships and efficient supply chains can enable industries to adopt sustainable hydrogen technologies to support global efforts for the reduction of carbon emissions and associated environmental impacts.
Krishnaveni Malladi is a Consultant (Hydrogen Technology) with the Sustainable Cities and Transport team at WRI India.