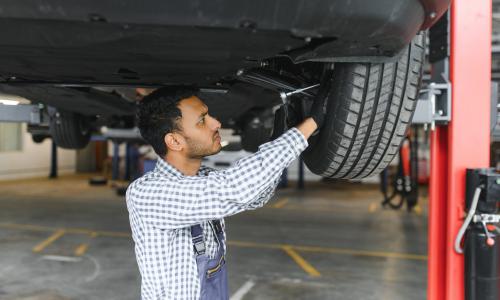
5 Ways the EV Transition is Changing Jobs in India’s Automotive Sector
India’s shift toward electric vehicles (EVs) is reshaping its automotive landscape. It is transforming jobs not just in manufacturing but also in servicing, logistics and fueling. This transformation could have profound implications for almost six million workers in micro, small and medium enterprises (MSMEs). Unlike original equipment manufacturers (OEMs), MSMEs may not have the resources to invest in new technologies, retrain their workforce and adapt quickly.
Understanding how this transition is unfolding is crucial to identifying the associated challenges and opportunities it presents. This blog looks at five crucial ways in which the EV transition is affecting jobs in India’s automotive sector.
1. Export Markets Are Shifting from ICE Vehicles to EVs
India is a key player in global automotive component exports, with MSMEs forming the backbone of global supply chains. Europe and the U.S., which account for 60% of India's automotive exports, are shifting towards EVs. As some of these countries aim for 100% EV sales by 2035, demand for traditional internal combustion engine (ICE) parts – such as fuel injectors and transmission systems – in these high-value markets will decline. To sustain exports, India will need to explore newer markets, such as Africa, the Commonwealth of Independent States (CIS) and the Baltics, where EV adoption is slower and exports are growing.
Indian MSMEs risk losing key export markets unless they adapt to the growing demand for EV components, such as electric motors, batteries and power electronics. Alternatively, they must secure comparable export revenues in emerging markets. Access to finance, technical expertise and workforce upskilling will be necessary for these businesses to remain competitive in the global automotive supply chain.
2. EV Manufacturing is Expanding Beyond Traditional Automotive Hubs
Tamil Nadu, Maharashtra and National Capital Region (NCR) have historically been home to some of India’s largest auto-component manufacturers of ICE vehicles. However, EV-focused policies, targeted subsidies and competitive incentives are driving the emergence of new EV manufacturing hubs in Gujarat, Uttar Pradesh, Karnataka, Andhra Pradesh and Telangana, attracting both domestic and global players. Policy support, lower operating costs, improved infrastructure, access to a skilled workforce and heavy investments in the EV ecosystem – including battery production and charging stations – are further encouraging automakers to look beyond traditional hubs. States like Gujarat and Karnataka are offering tax breaks, land incentives and simplified regulatory processes, making them attractive destinations for major EV manufacturers and suppliers.
This shift is creating new economic opportunities and jobs across India. However, traditional auto hubs risk losing economic opportunities in the short term unless they invest in preparing their local ecosystem for EV manufacturing and adoption.
3. EV Charging Infrastructure is Expanding but Requires Fewer Workers
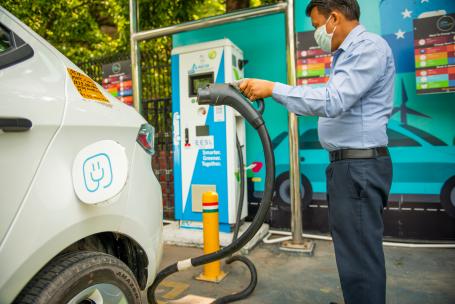
India’s petrol pump industry currently employs over 1.5 million people across over 80,000 stations. As the share of EVs increases, demand for petrol and diesel will decrease, reducing the number of fuel stations and jobs. EV charging stations, which require fewer workers due to automation or self-service, are expected to replace fuel stations — a trend already observed in some countries.
EV charging stations in India have significantly lower entry barriers than traditional fuel stations. They require less capital investment, as they don’t need large land parcels or complex infrastructure like underground fuel tanks. India’s FAME II scheme and various state EV policies further encourage new entrants and small businesses by providing subsidies, tax benefits and reduced electricity tariffs. Unlike fuel stations, EV chargers can be installed in malls, shopping centers, office complexes and residential communities, offering far greater location flexibility.
Additionally, retraining programs are crucial for mitigating job losses and leveraging new opportunities in the EV sector, especially for informal workers. These new roles could include managing charging stations, maintaining EV infrastructure or jobs in the renewable energy sector. Without reskilling initiatives, a significant portion of the petrol pump workforce stands to face displacement.
4. EV Servicing and Repairs is Replacing Traditional Repair Work with Specialized Roles
India’s car repair sector employs about four million people, particularly in small, family-owned garages and informal businesses. As EVs require fewer moving parts, as compared to ICE vehicles, traditional services like oil changes and engine repairs will become obsolete.
Additionally, EV maintenance requires specialized knowledge and skills, including battery management, electric powertrain servicing and software updates. OEMs and authorized service centers are increasingly handling EV repairs, reducing the need for roadside repair shops. Traditional repair businesses will need to invest in new tools, equipment and training to adapt to these changes. This shift may be especially difficult for small garages that have limited resources. Without support and retraining programs, many businesses could face financial strain while workers run the risk of losing jobs unless they are upskilled and employed by the OEMs.
5. Women are Joining the Automotive Manufacturing Workforce

Historically, women have been underrepresented in technical roles within India’s automotive manufacturing sector, especially in ICE vehicle production. However, the transition to EVs is creating new opportunities for women. Manufacturers are increasingly hiring more women in assembly lines, engineering and operations management, recognizing their precision skills, higher dexterity and lower attrition rates. A notable example is Ola Electric’s women-only manufacturing unit in Tamil Nadu. EV companies such as Mahindra Electric, Kinetic Green, Ather and others are actively working to increase women’s participation both in operations as well as leadership.
Unlocking the full potential of EV manufacturing for women requires the industry to focus on skill development, policy support and equitable career pathways. Targeted upskilling in EV technologies can equip women with future-ready skills. Inclusive workplace policies —ergonomic shop floors, safe transportation and childcare — can further foster a supportive environment. Strengthening social protections, including maternity benefits and flexible work arrangements, is crucial for retaining women in the workforce and ensuring long-term gender equity in the sector.
Placing People at the Center of the EV Transition
The shift from ICE vehicles to EVs presents challenges and opportunities for India’s automotive sector. Although MSMEs, petrol pump workers and small repair businesses may face disruptions, the transition has the potential for inclusive growth and job creation, particularly in emerging manufacturing hubs and the EV infrastructure sector. A just and people-centered EV transition must focus on reskilling workers, supporting small businesses and proactive regional transition planning to develop a robust local EV ecosystem. By fostering an inclusive and skilled workforce, India can successfully navigate this transition while creating opportunities for all.